Making Carbon Fiber Body Panels: The Future of Automotive Customization
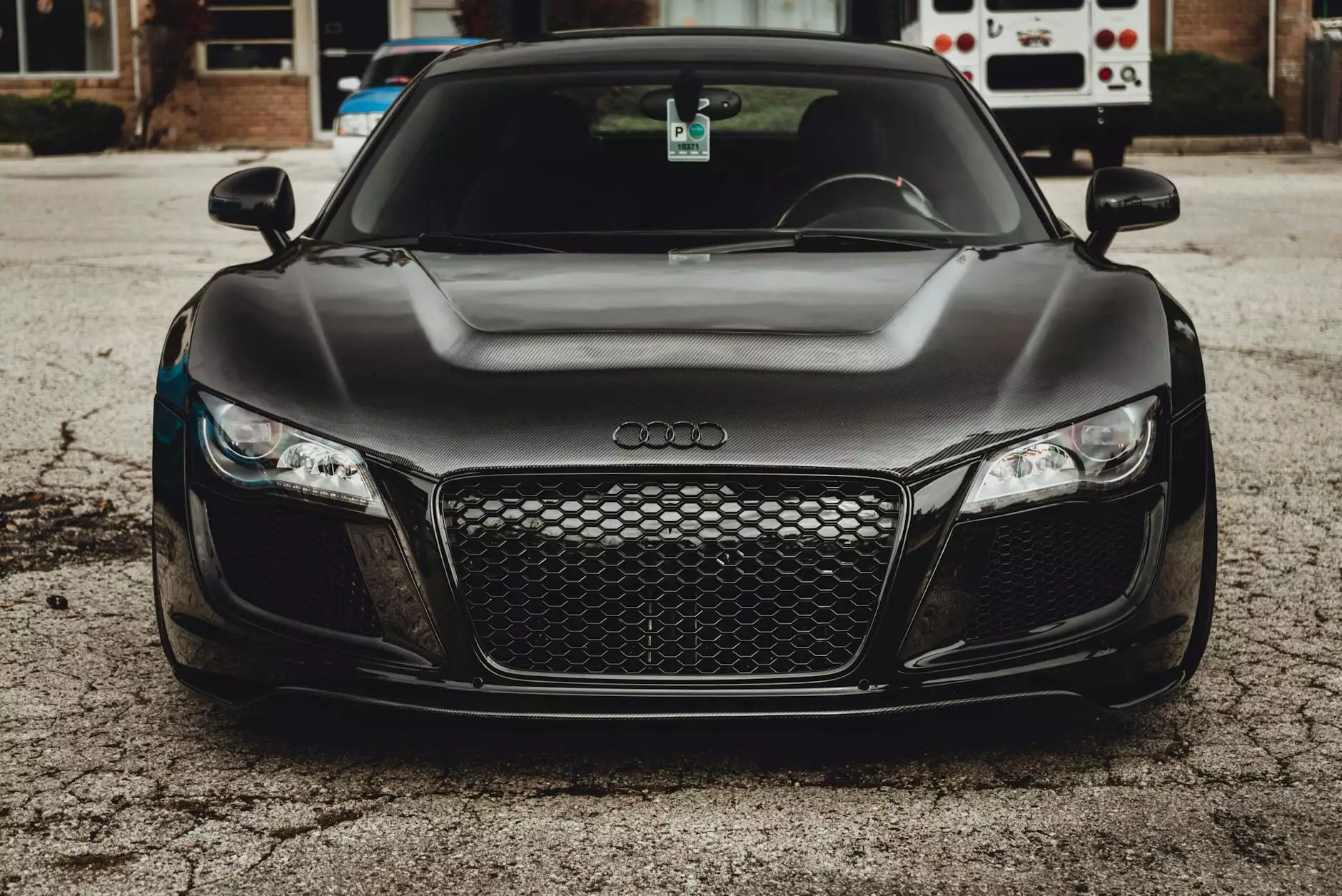
Carbon fiber body panels represent a significant advancement in the automotive industry, combining strength, lightweight properties, and aesthetics. In this article, we will delve deeply into the process of making carbon fiber body panels, its benefits, applications, and the future it holds for auto customization and performance.
What is Carbon Fiber?
Carbon fiber is a high-performance material made from thin strands of carbon atoms. The fibers are woven together, resulting in a fabric that is incredibly strong yet light. Carbon fiber is characterized by its remarkable tensile strength and rigidity, making it an ideal choice for high-performance automotive applications.
The Advantages of Carbon Fiber Body Panels
When it comes to customizing vehicles, making carbon fiber body panels offers numerous advantages, such as:
- Weight Reduction: Carbon fiber is significantly lighter than metals like steel or aluminum. Reducing weight in vehicles leads to improved handling, acceleration, and fuel efficiency.
- Enhanced Durability: Carbon fiber panels resist corrosion and are less prone to dents and scratches compared to traditional materials.
- Aesthetic Versatility: With a sleek, modern look, carbon fiber allows for creative freedom in automotive design.
- Improved Performance: The structural integrity of carbon fiber enhances a vehicle's frame, improving overall performance.
Understanding the Process of Making Carbon Fiber Body Panels
Step 1: Design and Prototyping
The journey of making carbon fiber body panels begins with meticulous design. Engineers and designers create 3D models using CAD (Computer-Aided Design) software. This stage involves:
- Defining specifications based on the vehicle’s performance and aesthetic requirements.
- Creating a prototype model to visualize the final product.
- Conducting simulations to test the aerodynamic properties of the design.
Step 2: Preparing the Mold
Once the design is finalized, the next step is to prepare a mold. Molds are typically made from strong materials such as aluminum or fiberglass. The mold may undergo textured finishes to ensure the surface of the carbon fiber panel matches the desired aesthetic. Preparation is crucial as it will also define the quality of the final part.
Step 3: Layup Process
During the layup process, sheets of carbon fiber fabric are carefully layered onto the mold. This process includes:
- Cutting Fabric: Carbon fiber fabric is cut into specific shapes and sizes that correspond to the mold.
- Resin Application: A resin is then applied to the fabric for adhesion. The type of resin influences the final characteristics and performance of the body panels.
- Layering: Multiple layers are added to achieve the desired thickness and structural integrity.
Step 4: Curing the Composite
The next critical step involves curing the composite in an oven or autoclave. During this process:
- The heat and pressure enhance the bonding of the resin and carbon fiber.
- This step solidifies the structures and develops their unique property characteristics.
- Curing times can vary based on the type of resin used and the desired strength.
Step 5: Trimming and Finishing
After curing, the carbon fiber panel is carefully removed from the mold. The panel may require:
- Trimming: Excess material is trimmed to fit precisely on the vehicle.
- Surface Finishing: The surface may be polished or coated to enhance its appearance and durability.
- Quality Control: Inspection is crucial to ensure the panel meets all performance specifications.
Applications of Carbon Fiber Body Panels in Automotive
The applications of carbon fiber body panels are numerous, revolutionizing the automotive landscape:
- Performance Cars: High-end manufacturers like Ferrari, Lamborghini, and McLaren use carbon fiber to enhance speed and efficiency.
- Luxury Vehicles: Many luxury brands incorporate carbon fiber to elevate the quality and aesthetics of their cars.
- Motorsports: In racing, every fragment counts. Carbon fiber is extensively used to build lightweight components that provide competitive advantages.
- Custom Builds: Car enthusiasts and custom builders are increasingly turning to carbon fiber for bespoke projects, creating lightweight and unique vehicles.
Challenges in Making Carbon Fiber Body Panels
While the advantages are significant, the process of making carbon fiber body panels is not without its challenges:
- Cost: The raw materials and production methods can be expensive, making it a significant investment for some businesses.
- Complex Workflow: The processes involved require specialized knowledge and skills.
- Environmental Concerns: As with many composites, carbon fiber production raises questions regarding sustainability and recyclability.
Future of Carbon Fiber in Automotive Industry
The future of making carbon fiber body panels seems promising. Continuous advancements in technology are helping to lower costs, improve manufacturing efficiency, and develop more sustainable practices. The integration of carbon fiber with other materials will also open new doors for innovation.
Innovation through Automation
Automation in the manufacturing process is revolutionizing the production of carbon fiber components. Automated layup machines and robotic systems can increase precision and reduce labor costs, paving the way for broader adoption and new applications.
Expanded Applications
As the technology matures, we can expect to see carbon fiber body panels in a wider range of vehicles, including mainstream automobiles, not just high-performance or luxury cars. This shift could democratize high-end materials, granting access to performance benefits to a larger market.
The Environmental Impact of Carbon Fiber Production
While carbon fiber panels provide numerous benefits, manufacturers are increasingly focusing on addressing environmental concerns associated with production. Efforts include:
- Improved Recycling Techniques: Developing processes to recycle carbon fiber waste is crucial in reducing the industry's carbon footprint.
- Sustainable Materials: Researchers are exploring the use of bio-based resins and other materials as alternatives to traditional petroleum-based products.
- Energy Efficiency: Innovations aimed at reducing energy consumption in production are essential for sustainability.
Conclusion: A Bright Future for Carbon Fiber Body Panels
In conclusion, the process of making carbon fiber body panels is an exciting frontier in the automotive world. As the industry continues to evolve with technological advancements and a drive toward sustainability, we can look forward to an ever-expanding role for carbon fiber in automotive design and functionality.
For both enthusiasts and manufacturers, embracing this innovative material means unlocking new performance potential and creating visually stunning vehicles. Companies like Tuneverse.net are at the forefront of this movement, pushing boundaries with customization and high-performance auto parts.