CNC Precision Machining Parts Factory: A Cornerstone of Modern Manufacturing
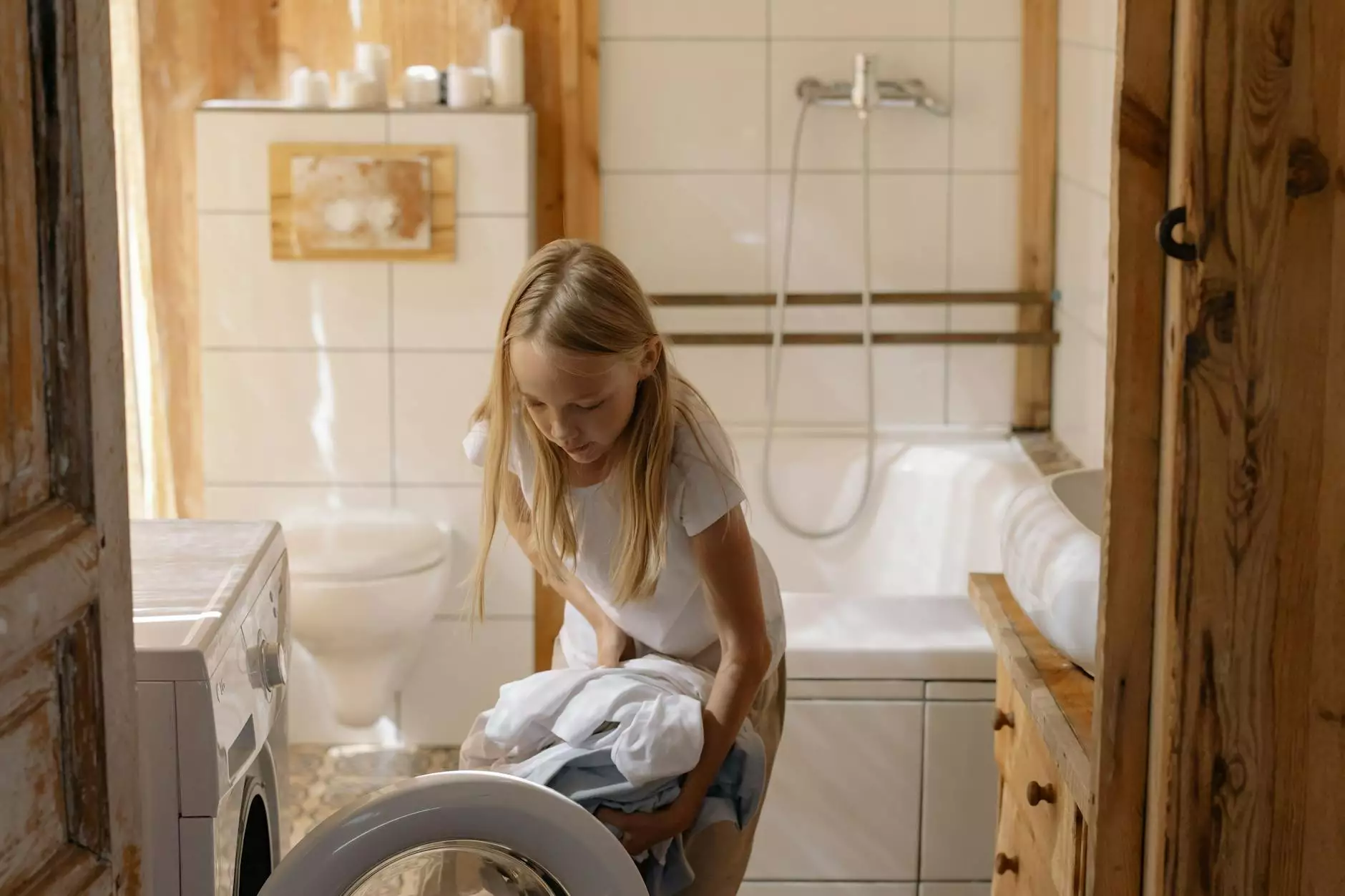
CNC precision machining parts factories play a crucial role in various industries, from aerospace to automotive, by providing high-quality, precise components that meet exacting standards. As technology continues to evolve, these factories are at the forefront of innovation, offering advanced manufacturing solutions that are both efficient and reliable.
What is CNC Precision Machining?
CNC, or Computer Numerical Control, refers to the automation of machine tools through computers executing pre-programmed sequences of machine control commands. This process allows for the production of highly precise components and parts with minimal human intervention. Precision machining itself is a process that involves the removal of material from a workpiece to create a finished part that meets strict tolerances and specifications.
The Importance of CNC Precision Machining Parts Factories
In today's fast-paced manufacturing landscape, the demand for precision parts is higher than ever. CNC precision machining parts factories are essential for several reasons:
- High Precision: CNC machinery can achieve tolerances of ±0.001 inches or better, making it ideal for industries requiring precision.
- Consistency: Once programmed, CNC machines can produce identical parts, ensuring uniformity across large production runs.
- Complex Designs: CNC machining allows the creation of intricate designs that would be difficult or impossible to achieve with traditional machining methods.
- Material Versatility: These factories can work with a wide range of materials, including metals, plastics, and composites, broadening their application scope.
The CNC Precision Machining Process
The process of CNC precision machining typically involves several key stages:
1. Design and Prototyping
The first step involves creating a detailed design of the part using CAD (Computer-Aided Design) software. This design is essential as it guides the machining process.
2. Programming
Once the design is finalized, it is translated into a machine-readable format using CAM (Computer-Aided Manufacturing) software. This software generates the instructions that the CNC machine will follow.
3. Material Selection
The appropriate material is chosen based on the part's intended use, mechanical properties required, and cost considerations. Common choices include metals such as aluminum, steel, and titanium, as well as plastics.
4. Machining
During this phase, the CNC machine begins cutting, drilling, or milling the material according to the programmed instructions. This step requires precision, and CNC machines often employ advanced tools such as end mills, lathes, and routers.
5. Finishing
Once the machining is complete, the parts may undergo various finishing processes such as polishing, anodizing, or painting to improve their appearance and functionality.
6. Quality Control
A rigorous quality control process ensures that every part produced meets the specified tolerances and quality standards. This may involve various inspection methods, including CMM (Coordinate Measuring Machine) inspections and visual checks.
Benefits of Partnering with a CNC Precision Machining Parts Factory
Companies can reap numerous benefits by collaborating with a proficient CNC precision machining parts factory such as Deep Mould:
- Cost Efficiency: CNC machining reduces waste and improves production speed, leading to lower manufacturing costs.
- Short Lead Times: Advanced CNC factories can significantly reduce lead times, allowing for quicker market entry.
- Expertise and Support: Partnering with experienced factories provides access to knowledgeable engineers who can assist with design optimization and production planning.
- Scalability: As demand increases, CNC precision machining parts factories can easily scale operations to meet higher production volumes.
Industries That Benefit from CNC Precision Machining
The versatility of CNC precision machining means that numerous industries benefit from its application:
Aerospace
Aerospace components require high levels of precision and quality. CNC machining is critical in producing parts such as fuel nozzles, turbine blades, and landing gear components.
Automotive
The automotive industry relies on CNC machining for the production of engine components, transmission parts, and various fixtures. High precision ensures optimal performance and safety.
Medical Devices
In the medical field, CNC precision machining is vital for creating surgical tools, implants, and other devices. These parts must meet stringent regulatory standards.
Electronics
The electronics industry uses CNC machining for the fabrication of enclosures, connectors, and other components that require fine tolerances to function effectively.
Challenges in CNC Precision Machining
While CNC precision machining offers tremendous advantages, it is not without its challenges:
- Initial Investment: High-quality CNC machines and technologies can require significant upfront investment, which may be a barrier for smaller companies.
- Skilled Labor Requirement: Operating CNC machinery requires skilled technicians who can program, troubleshoot, and maintain the machines.
- Material Limitations: Certain materials can be challenging to machine and may require special tooling or processes.
The Future of CNC Precision Machining
The future of CNC precision machining looks bright, with continuous innovations shaping the industry:
1. Automation and Robotics
The integration of automation and robotics is set to further enhance the efficiency of CNC precision machining factories. Automated material handling and robotic tools can optimize workflow.
2. Advanced Materials
As new materials, such as composites and advanced alloys, are developed, CNC machining technologies will adapt to accommodate these versatile options.
3. Smart Manufacturing
The rise of Industry 4.0 and smart manufacturing will introduce AI and IoT (Internet of Things) technologies to enable predictive maintenance and enhance machine efficiency, resulting in higher quality outputs.
4. Sustainability
There will be a growing emphasis on sustainability within CNC precision machining, focusing on reducing waste, reusing materials, and employing energy-efficient practices.
Conclusion
In summary, the CNC precision machining parts factory holds a pivotal place in modern manufacturing. Its ability to produce complex, high-quality parts with unparalleled precision has transformed various industries. As companies like Deep Mould continue to enhance their capabilities, the future looks promising for CNC machining, ensuring that it remains a critical component of manufacturing excellence.